Sculptors and metalworkers alike uncover hidden beauty within raw materials, as Michelangelo famously noted. Lost wax casting and Forging, ancient techniques, epitomise this artistry, shaping metal into intricate forms. Lost wax casting excels in precision, crafting detailed shapes from molten metal in wax moulds. Forging, conversely, emphasizes strength, compressing metal to enhance durability. Understanding the nuances of each method is crucial for informed decision-making in metalworking projects
What is Lost Wax Casting
Lost wax casting, or Investment Casting, blends ancient tradition with modern precision and flexibility. It starts with a wax replica of the desired part encased in refractory material to create a mould. Once the wax is melted away, molten metal fills the void, yielding intricate final products. Materials range from bronze to steel, offering versatility for industries like aerospace industry, Automotive Parts, and construction machinery. Despite its precision, lost wax casting can be time-consuming and costly for mass production. Yet, for intricate designs requiring detail and material variety, it remains unmatched.

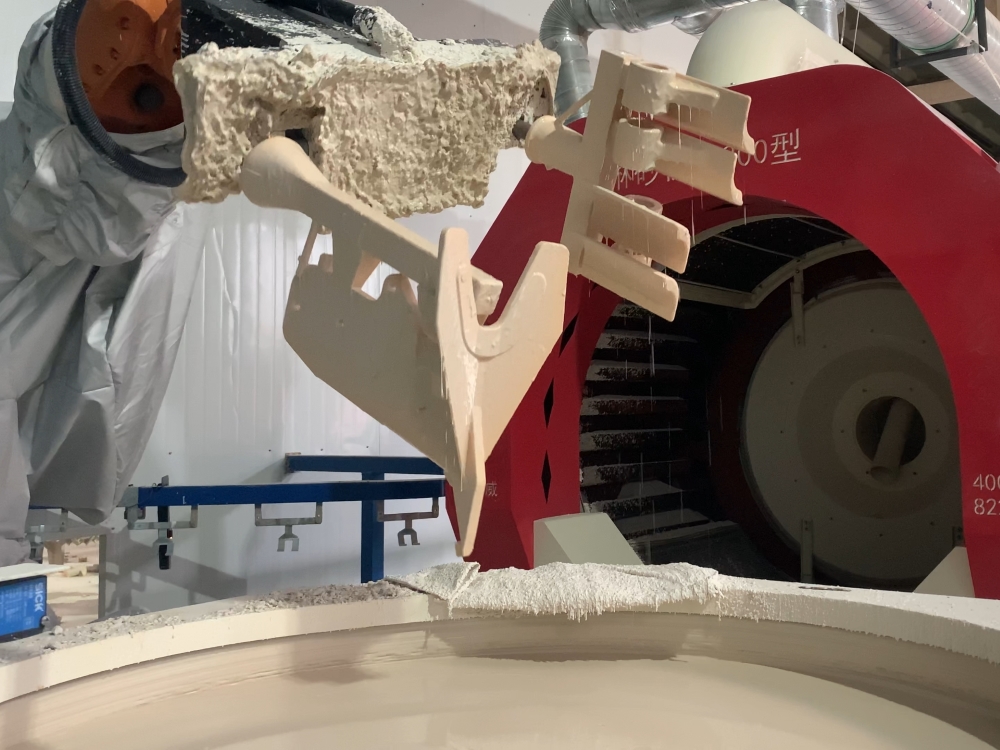
Overview of Forging
Forging, a time-honoured method of shaping metal, remains a cornerstone of manufacturing. It involves compressive forces to shape metal, typically with a hammer or die. Materials range from steel to titanium, chosen for specific properties like strength and ductility. Used in automotive, aerospace, and construction, forging excels in producing high-strength components like forged shafts, crankshafts and gears. Its key strength lies in enhancing metal durability and toughness through grain alignment. However, forging may not suit intricate shapes and requires subsequent machining, which can increase costs and time.
Comparing Quality and Precision
In manufacturing, achieving quality and precision is paramount. Lost wax casting excels in precision, replicating intricate details with accuracy. It's ideal for components requiring exact dimensions and aesthetic detail, like aerospace parts and sculptures. Forging, though less precise, enhances metal quality, imparting exceptional strength and durability. Its refined grain structure ensures robustness, making it vital for heavy machinery and structural applications. The choice between the two methods depends on project requirements: precision for lost wax casting and strength for forging.
Strength and Durability
Strength and durability are crucial in metalworking processes. Forging excels in enhancing metal strength by realigning its grain structure through compressive forces. This makes forged parts robust, ideal for heavy-duty machinery and engine components. In contrast, lost wax casting offers precision and versatility but doesn't inherently strengthen metal like forging does. Strength in cast parts depends on material choice. Despite this, advancements in materials science have improved the strength of cast components, narrowing the gap between casting and forging in certain applications.
Cost and Production Time
Cost-effectiveness and efficiency are crucial in manufacturing. Lost wax casting and forging have distinct cost implications and time requirements. Lost wax casting, while precise and high-quality, is time-consuming and costly due to its intricate process. Creating wax models, making moulds, and casting demand significant time and labour. Materials used, especially specialised metals, add to costs. It's ideal for custom or specialised parts where precision is valued over cost. Conversely, forging is more cost-effective for large-scale production. Despite initial setup costs, it's faster, especially for standardised parts. Forged components are durable, leading to long-term savings. It's preferred for high-volume, standardised production in automotive and industrial machinery. Factors like part complexity, material, and volume influence costs and production time. Technological advancements have improved both processes, reducing costs and production times.